The image of an ultra-energy efficient house typically calls to mind images of buildings that are also ultra-modern in design. Very square structures, with flat roofs, steel siding, glass, and a general “boxy” look about them. Something like the images in the pictures below.
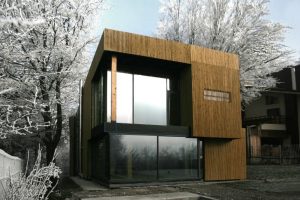
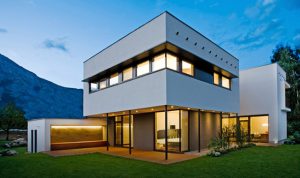
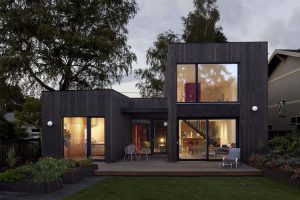
These houses certainly have their appeal, and many people love very modern structures for their simplicity and their ability to stand out among the crowd. They can also be a great way to keep construction costs reasonable. Simple shapes and flat roofs can be very quick and inexpensive to construct, which can help offset some of the costs of upgrading the envelope to a higher standard. However, to some people, something so different just doesn’t fit their idea of a “home.” Fortunately, it is possible to build a super-efficient home with a much more conventional look. Pheasant Hill Homes had just such an opportunity in Qualicum Bay.
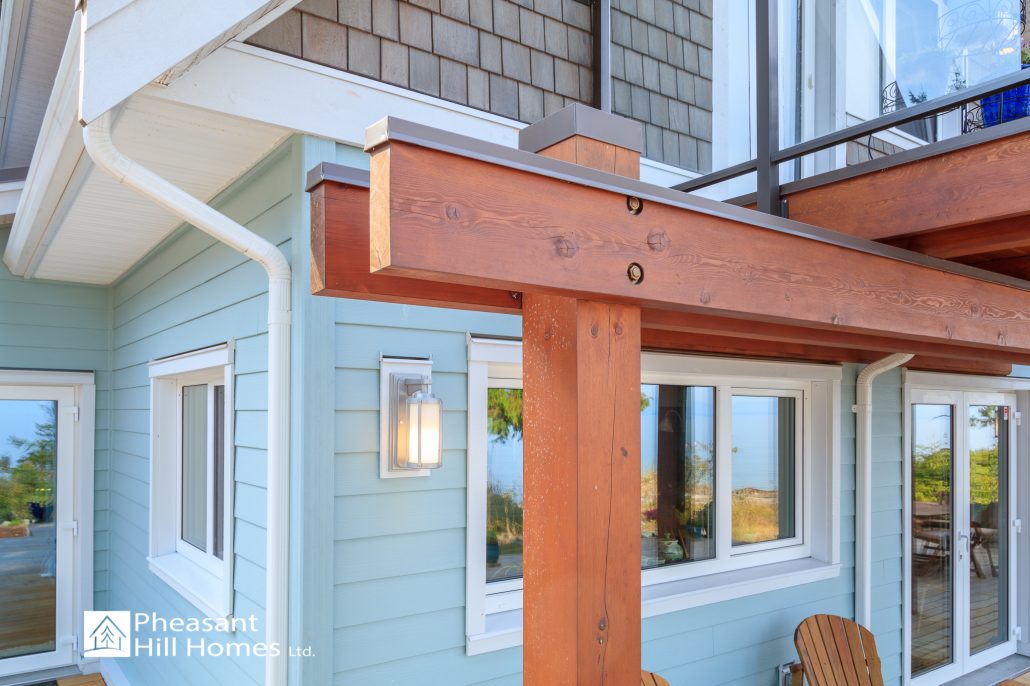
On a quiet stretch of beach midway along Vancouver Island, there now stands a new craftsman style house, with some updated elements suiting its waterfront location. Its steep-sloped roofs, long shed dormer on the upper floor, simple but pronounced exterior trim and lap siding mixed with shingled gables recalls an iconic past, and provides a comforting sense of familiarity. But because of it’s beautiful beachfront setting only 60 feet away from the water, it is supplemented with a glass-railing upper deck off the master bedroom and an expansive 1200sq.ft. ground level deck to enjoy the sun and surf. Designed by architect Bruce Fleming-Smith (MRAIC) of Oceanside Design, the home tidily fits the style and needs of the homeowner.
However, behind this familiar façade is one of the most energy efficient houses in Canada. While uncertified, the house was detailed to have an envelope that adhered very closely to the Passive House criteria, which is acknowledged as the most stringent energy efficiency building standard in the world. Its main goal is to aid designers and builders in creating buildings which use about 85% less heating and cooling energy, and total building energy usage of less than half of their new, code-built counterparts. Because the architect had taken the Passive House training, and carefully designed and detailed the plans to adhere to the standard, it was important to both he and the client that a builder be selected which was also conversant in the language of energy efficiency. Because Pheasant Hill Homes has three staff members whom have taken Passive House training through the Canadian Passive House Institute, we were a logical fit. Due to the depth of shared knowledge in this partnership, the house construction went very smoothly and successfully. With a steep learning curve, the early investment by team members in education is a critical piece to the success of such cutting edge projects.
Essentially, a super-insulated house needs three basic things to be successful:
- a very high R-value envelope to essentially wrap the building in a warm blanket of insulation,
- a very airtight envelope to reduce the loss of conditioned air out of the building
- a mechanical system that can efficiently heat (and/or cool) the space and provide a constant supply of fresh air without losing the energy put into that air to make it comfortable.
This house certainly had all three pieces of the puzzle.
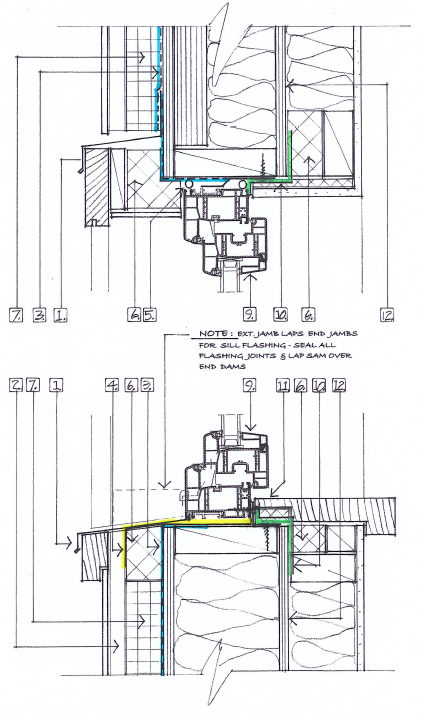
Copyright Bruce Fleming-Smith
With effective insulating values of R-38 walls, R-48 floors and an R-70 roof, the thermal properties of the house are double those of a new code-built residence. Essentially, the house is framed much like a conventional 2×6 structure, but on the inside surfaces of all the exterior walls and ceiling trusses, there is a layer of 5/8” OSB with all of the seams taped using a high-quality air-sealing tape by SIGA. This OSB (oriented strand board) layer acts as both the airtightness layer, and the vapour retarding layer. This outside structure (both wall and truss) was diligently insulated with dense-pack cellulose by Island Basement Systems Group.
Watch our video describing this insulation HERE or BELOW
Inside of those assemblies (both wall and ceiling), a secondary framed 2×4 cavity was built to house all of the wiring and plumbing required to run along the exterior of the building. While essentially a service chase, these assemblies were also insulated with fiberglass batts. On the outermost surface of the exterior walls, a thick layer of 2” Roxul Comfortboard 80 insulation is applied to ensure that there is no thermal bridging whatsoever through the exterior. Worth noting in this project, is that no matter how different the envelope appears in the drawings, from either side of the wall the finishes can project any kind of aesthetic desired. While the details are cutting edge, the finish can be totally conventional.
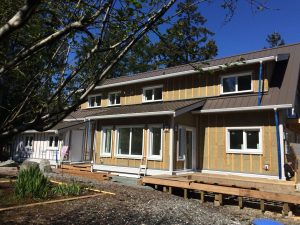

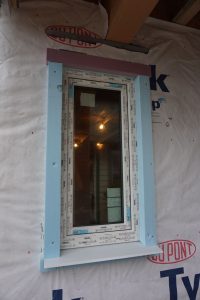
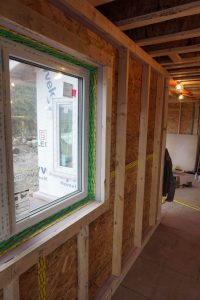
Part of the envelope efficiency is the inclusion of high performance windows and doors on the project. Supplied by Euroline Windows out of Victoria, BC, the 4700 Series units provide exceptional insulating, airtightness and watertightness ratings. With over R-7 for the operable units, they boast about triple the insulating value of a basic vinyl slider. Because all windows have such poor thermal performance compared to the walls in which they are placed, cheap windows can have a profound effect on the comfort and energy efficiency of a building. Dollar for dollar, the Euroline units provide exceptional value, and we are extremely fortunate to have them supplied by a company local to Vancouver Island.
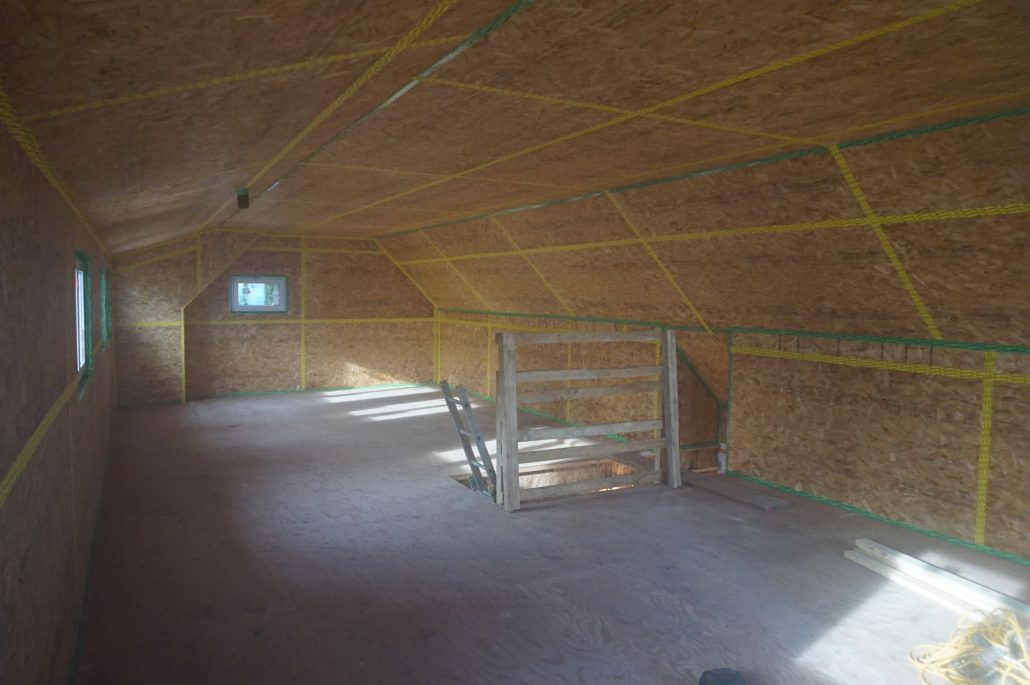
While the air sealing of one of the modern “boxes” from the top of this article is relatively straightforward, the unique challenges of a house with a much more complicated shape presented very unique challenges and demands during framing. Thinking creatively and methodically during the build to anticipate and solve problems before a window of opportunity was lost was crucial. Notably, because many of the upper floor walls did not stack perfectly above the lower floor walls, “zig-zagging” the air barrier at the floor and ceiling levels was often necessary. Accommodating the air barrier around imposing structural brackets supporting posts and beams for the floor system was also an exercise in deep thought! Achieving all of this while framing in the pouring rain and ice was a serious challenge. But, in spite of all the complexities in design and weather, our preliminary blower-door test (performed by E3 EcoGroup out of Vancouver) results came in at 0.19 ACH50. If you are an energy nerd, you will recognize that this is an incredibly air-tight building; three times tighter than the Passive House requirement of 0.6ACH50. If you are not an energy nerd, suffice it to say that it was recognized as the second most airtight building in Canada at the time of testing. The level of attention to the air barrier detailing in both the design and construction phases can ensure success or failure in the airtightness of a structure. You can’t win with just one or the other: both are equally imperative.
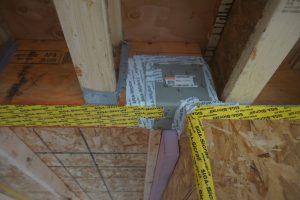
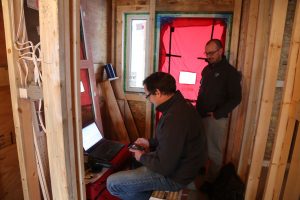
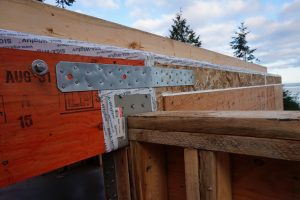
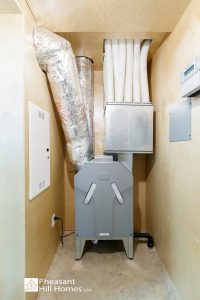
Because of the building’s incredible envelope, it requires very little heat to keep it warm. As a result, simple baseboard heaters were used for their low initial cost, their exceptional longevity and their need for zero servicing and maintenance. The ventilation system is the German manufactured Zehnder ComfoAir 200, which is the gold-standard of HRV’s. Using about the same electricity as a small lightbulb, the unit constantly ventilates the entire home, is barely audible, and transfers about 85% of the heat from one airstream to the other so that the energy spent to heat or cool your home is not wasted by being exhausted to the exterior.
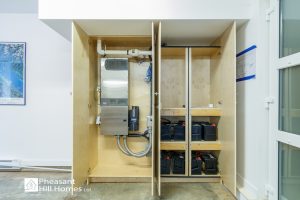
Battery Back-Up System
Accommodations were made for future inclusion of rooftop solar modules to offset some, or all of the home’s energy needs which have now been installed and connected to the owners battery back up system.
These kinds of simple mechanical systems lend themselves well to energy efficient assemblies. The thousands of dollars saved on expensive heating and cooling equipment can instead be spent on higher quality windows and doors, insulation levels or other efficiency upgrades.
The most notable aspect of this house, however, has nothing to do with all the technical details of the construction, the fancy ventilation system or the remarkable air-tightness. The most notable quality, is that you would never know that any of these things are there behind the siding and drywall. The house looks like any other conventionally styled craftsman house on the street. It doesn’t need to be a sleek, modern box, all glass, steel and concrete to be ultra-energy efficient. One can employ these leading edge energy efficiency techniques in any house of any design, and it will make a marked difference on the quality, comfort and low-operating cost of any home. For once, you can have your cake and eat it too, no matter what kind of cake you prefer!